With apologies (again) for a terrible pun-title, behold the latest update from the Auster maintenance team regarding progress on the reconditioning of our 1942 Auster Mk1.
With the mantra “There shall be no play in the control system”, the team have been inspecting every aspect of the Auster’s flying controls – including the horizontal flying trim system. This trim control is provided by a pair of trim tabs located beneath the tail plane. The tabs are controlled by the pilot independently of the elevator via two steel wires that run up the inside of the fuselage.
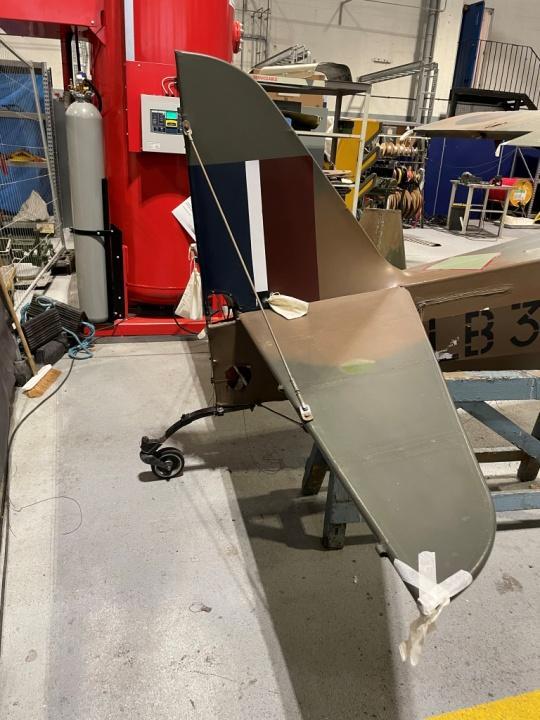
Auster Mk1 tail unit with rudder and elevators removed showing trim tab location – just forward of the tail wheel mount)
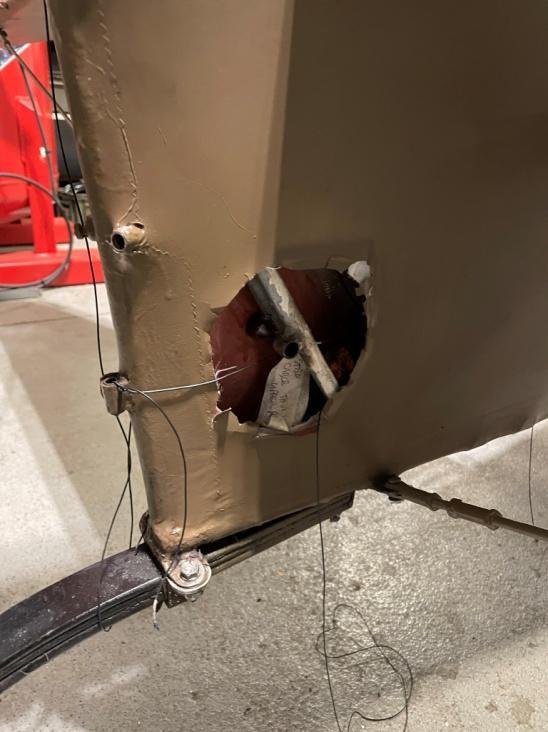
The trim tab spar is located through the fuselage here – with a control horn on the spar connecting to the pilot controls at the front of the ac
The inspection of this sub-system revealed significant wear/play at every mechanical interface so less the tabs themselves, everything is being replaced. Now with (significant) effort, some bits can still be sourced but as with many of the Auster’s engineering solutions, we have to make a few parts ourselves. Converting 40 feet of cold-drawn piano-wire into beautiful control cables with perfect eye-ends will be the subject of later update; for now we have a bent spar to sort out.
And it’s not just bent – it’s the wrong specification. The current spar looks like it may have served in a previous life as the central support for a 16th Century Pike wielded by some brave warrior. I can see what has happened though; at some stage, probably during ground handling, the original spar was bent or broken and a new item was required. I do have some sympathy/empathy with the engineer concerned as given the challenges encountered to find the right item, I’ll admit at one stage, I also was tempted to repurpose a bit of 3/8” mild steel stock as a solution.
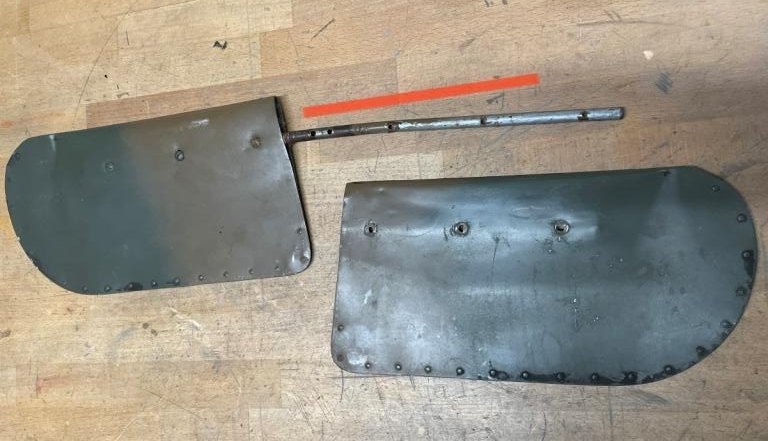
Auster Mk1 trim tabs with a bent spar
It turns out we needed some Spar-ing Partners to solve this problem. First up was good friend to the HAAF and Auster/Taylorcraft technical guru Ron Neal who provided a copy of the right drawing. Thanks Ron! And surprise suprise, the spar is a tube, not a bar – and the tube material specification was T35 alloy steel. Great – off we go in search of 3/8” T-35 tubing.
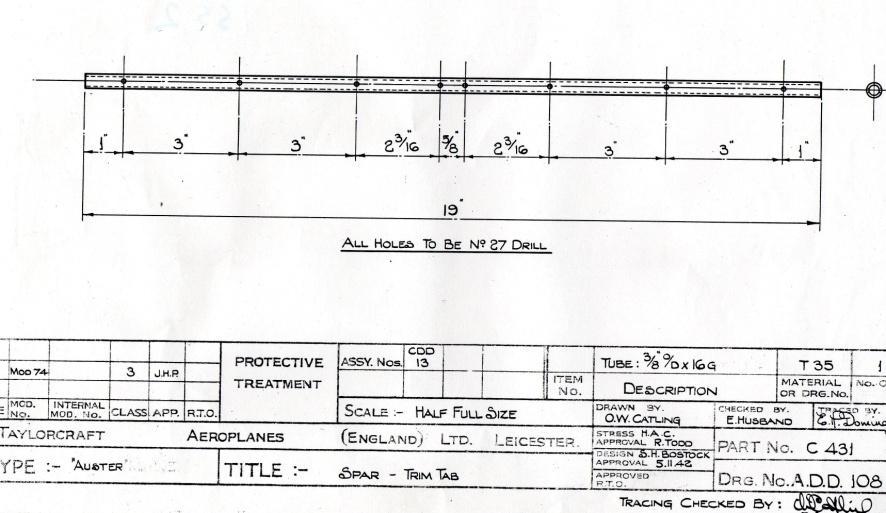
Copy of original 1942 drawing for Auster trim tab spar
So in 1942, T35 was a popular choice in aircraft manufacturing – but it doesn’t exist now and finding new T35 stock was quickly relegated to a “pipe-dream”. After a lot of internet trawling and with a ton of help from Phil at at ProFormance Metals Limited, we learn that the British Standard (BS) T35 tube specification was replaced by BS T64 tube in 1972. Phil, a fountain of knowledge on such matters, advised that the aerospace and racing manufacturers used a lot of T64 in the 80s and 90s. Great – may we have some T64 tube then please? Ahh; the manufacturing industry moved from T64 to an American spec (4130) years ago……..nobody makes T64 anymore; (although I did get a quote from another steel supplier to make us some at £40/m – provided we ordered at least 1,500 metres!!).
And then on the nth call searching for T64 tube, Aerocom Metals saves the day. He kindly checked their stock and said “we have a couple of T64 off-cuts at the mill – would a 3m length do the job”? With 3m of T64, we can make six spars – enough to provision for the next 300 years of operations, even with an occasional ground-handling incident. Haggling for (probably) the only length of 3/8” T64 tube in the world felt wrong so Phil named his (very reasonable) price – and we paid up. Many thanks Steve – you and Aerocom Metals knocked it out of the park!

Underlining the Taylorcraft (American) spec of the aircraft is that everything is in imperial sizes – so our final partner in this journey was a really helpful guy called Aron at CML Supply, Lexington (Kentucky) who sent us a pack of No 27 size Cobalt drill bits. This will enable us to drill the (quite hard) T64 tube with lovely 3.658 mm diameter holes (not a drill bit size normally carried in the tool box). The 4BA screws used to attach the trim tabs are 3.62 diameter so we will have a rather pleasing 38 thousandths of a mm clearance in the spar. There shall be no play in the control system!
Steve Harris
HAAF Engineering Manager